The injection of chemical treatments and sampling of process fluids are two major requirements for any corrosion control system. Often corrosion monitoring systems are selected to evaluate and optimize chemical injection performance. Axess provide systems that can be serviced online using the same retrieval tools used for corrosion monitoring devices, or fixed flanged systems. A range of quills and atomizing nozzles can be provided in many different materials. Wake frequency and atomization calculations are provided free of charge on every project managed by Axess.
Chemical Injection and Sampling
Whilst many injection and sampling systems can only be serviced and maintained during shutdown conditions Axess provides a range of high and low-pressure injection and sampling systems which can be serviced safely online at pressures up to 6,000 PSI / 413 Bar and temperatures up to 232°C / 450°F. Retrieval tools and some spare parts are common with the corrosion monitoring equipment using the same access system. Costs can therefore be reduced.
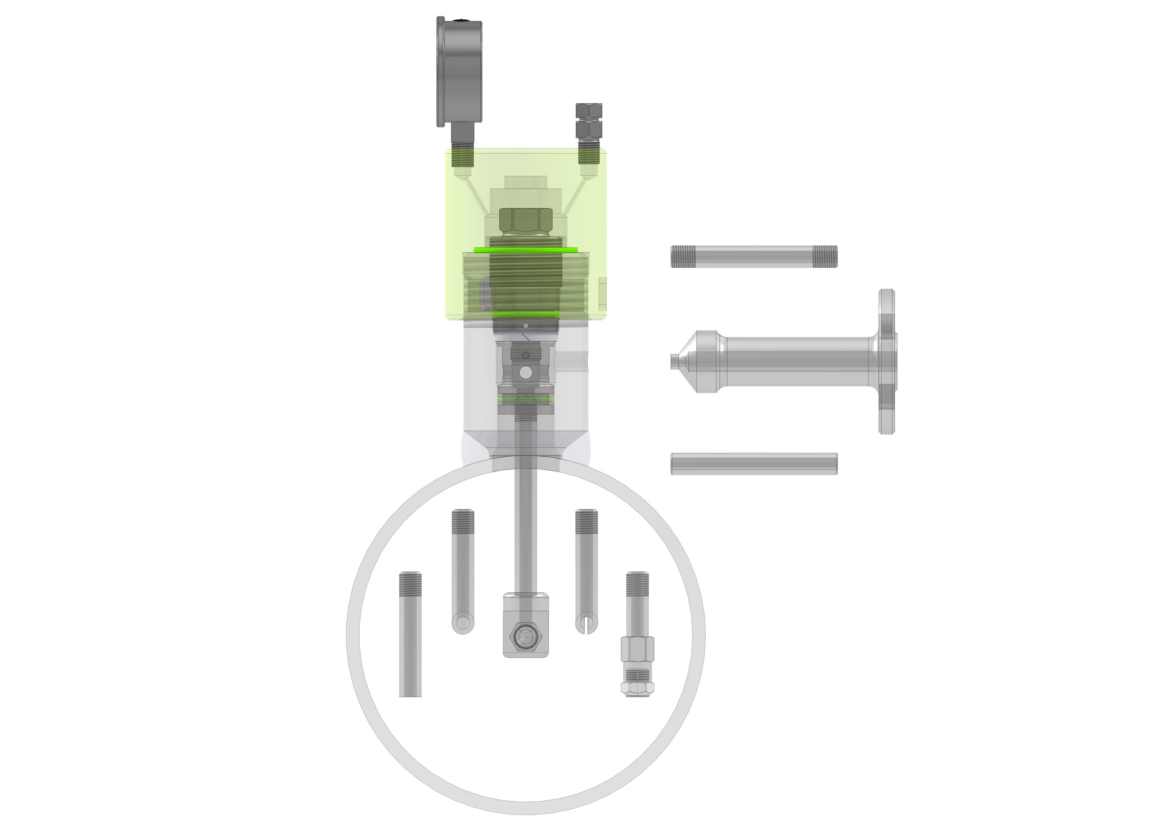
Direct Injection
The Axess Direct Injection system provides an alternate solution allowing the use of non-tee fittings whilst still maintaining the safety, reliability, and online servicing capability of our side tee systems including secondary isolation with pressure retaining cover. These fittings provide the flexibility to repurpose existing monitoring fittings or allow installation of new injection points at critical locations where space may be restricted.
The Direct Injection system incorporates two internal one way check valves built into a Hollow Plug. This allows chemical to be injected into the line through the center of the plug, and prevents flowback of process into the injection line.
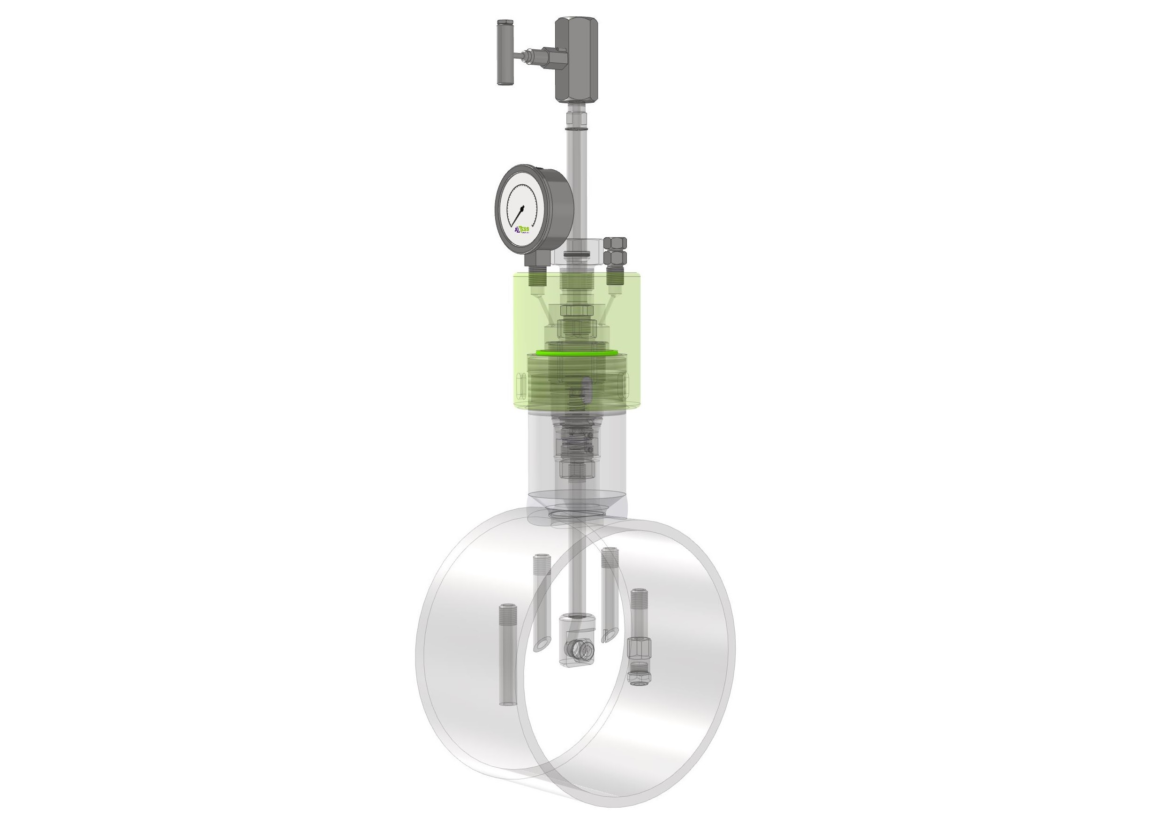
“Great to work with this team on all of our corrosion monitoring for our customer. They provide very prompt feedback to all of our questions. They are well versed in the equipment they supply. Looking forward to the continued support from Axess.”
H.E
Baker Hughes
Kickstarter
There is a lot to consider when specifying an Injection & Sampling system. With tens of thousands of product variations and variables to navigate it can seem like a daunting process.
Axess’ Kickstarter Program was developed as a tool to assist with generating part numbers and bills of materials, provide customers with an online platform for submission of requests for quotation and to help people get started in the industry.
Register with Axess for a Kickstarter login and make life less stressful.